Durch die Arbeit mit einem hochtransluzenten Zirkonoxid mit mehrschichtigem Farbverlauf (Multi-Layered) lässt sich die Effizienz im Dentallabor deutlich erhöhen. Den hervorragenden lichtoptischen und mechanischen Eigenschaften dieser Zirkonoxide (z. B. KATANA™ Zirconia Multi-Layered Produktfamilie, Kuraray Noritake), ist es zu verdanken, dass naturgetreue Restaurationen ganz ohne oder lediglich mit einer minimalen vestibulären Schicht Verblendkeramik gefertigt werden können. Dadurch lässt sich gegenüber der manuellen Verblendung von klassischen Gerüsten aus Zirkonoxid viel Zeit einsparen. Gleichzeitig ermöglicht der Ansatz eine reduzierte Wandstärke, die speziell im Zusammenhang mit minimalinvasiven Behandlungen erstrebenswert ist. Doch wie lässt sich das Potenzial der Multi-Layered-Materialien gänzlich nutzen und welche Faktoren beeinflussen die optischen Eigenschaften?
Um das hohe ästhetische Potenzial und die ausgewogenen Eigenschaften der modernen Zirkonoxide voll ausschöpfen zu können, ist es notwendig, die Restaurationen unter optimalen Bedingungen zu verarbeiten. Grundsätzlich gilt, dass die hochentwickelten Materialien mit ihrer hohen Transluzenz am anfälligsten sind, z. B.
- gegenüber Verunreinigungen während und nach der Nassbearbeitung,
- etwaigen Verschmutzungen im Sinterofen sowie
- mögliche Temperaturschwankungen während des Sinterns.
Mögliche Folgen sind beispielsweise ein Grauschimmer der Restauration und eine reduzierte Farbsättigung, Spuren von grüner, gelber, blauer oder grauer Farbe, weiße Flecken auf der Oberfläche und Abweichungen hinsichtlich Farbe sowie Transluzenz. Regelmäßig vorgenommen, beugen die nachfolgend beschriebenen Maßnahmen der Entstehung dieser Effekte vor. Dadurch unterstützen sie den Anwender in der Erzielung konstant guter Ergebnisse.
Optimierung des Fräsvorgangs
Spuren einer bläulichen oder gräulichen Verfärbung in der Zirkonoxid-Restauration sind in der Regel auf eine Verschmutzung des für die Nassbearbeitung verwendeten Kühlwassers mit extrinsischen Partikeln zurückzuführen. Eine solche Nassbearbeitung erfolgt vornehmlich in Chairside-Systemen. Meist sind nach der Verarbeitung von Glas- bzw. Silikatkeramik in der Fertigungseinheit verbliebene Siliziumoxid-Partikel die Ursache des Problems. Dieses lässt sich durch eine sorgfältige Reinigung der Fräskammer, des Wassertanks sowie des Filters der Anlage vor jedem Materialwechsel vermeiden. Alternativ ist es möglich, das Zirkonoxid trocken zu verarbeiten. Dies bringt auch weitere Vorteile mit- z. B. eine kürzere Verarbeitungszeit und eine bessere Rand- sowie Oberflächenqualität.
Dekontamination des Keramikofens
Generell sollte die Brennkammer eines Sinterofens vor jedem Sintervorgang gereinigt werden. Zu den wichtigen Maßnahmen zählen das Entfernen von Staub in der Kammer und die Reinigung der Heizelemente mit einer weichen Bürste. Auf den Einsatz von Druckluft sollte verzichtet werden.
Unerwünschte optische Effekte, die auf Restaurationen durch eine kontaminierte Brennkammer entstehen können, sind beispielsweise weiße Flecken auf der Restaurationsoberfläche, eine bläulich-graue Färbung und geringe Farbsättigung sowie grüne oder gelbe Farbspuren im Material. Weiße Flecken auf der Restaurationsoberfläche sind in der Regel ein Hinweis auf kontaminierte Sinterperlen aus Aluminiumoxid oder auf die Verwendung ungeeigneter Instrumente bei der Oberflächenbearbeitung sowie dem Abtrennen der Anstiftelemente. Diese Effekte sind durch den regelmäßigen Austausch der Sinterperlen vermeidbar (Abb.1). Auszutauschen sind sie mindestens einmal pro Monat, sobald sie beginnen, sich zu verfärben. Für die Nachbearbeitung vor dem Endsintern sollten ausschließlich feinkörnige Diamantinstrumente eingesetzt werden.
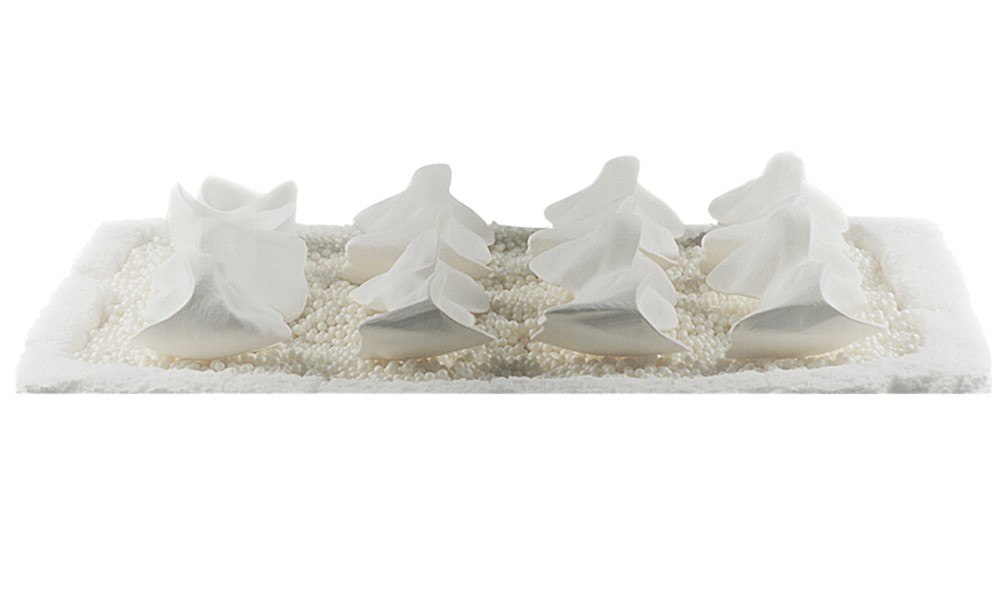
(Abb.1) Werden Sinterperlen aus Aluminiumoxid nicht regelmäßig ausgetauscht, können sie Ursache für weiße Flecken auf der Restaurationsoberfläche sein.
Eine bläulich-graue Färbung und geringe Farbsättigung ist mineralischen Rückständen von Färbeflüssigkeiten in der Brennkammer zuzuschreiben. Sie lassen sich durch einen Dekontaminationsbrand sicher entfernen. Dafür wird des Dekontaminationsprogramm am Ofen ausgewählt und die Brennkammer mit einigen Resten hochtransluzenter, nicht eingefärbter Zirkonoxid-Blanks bestückt. Nach Abschluss des Dekontaminationsbrands lässt sich an der Farbintensität der ursprünglich weißen Zirkonoxid-Stücke (Abb.2) erkennen, ob ein zweiter Dekontaminationsbrand erforderlich ist. Zur Vorbeugung bläulicher-grauer Verfärbungen an Restaurationen sollte ein solcher Brand mindestens einmal monatlich durchgeführt werden.
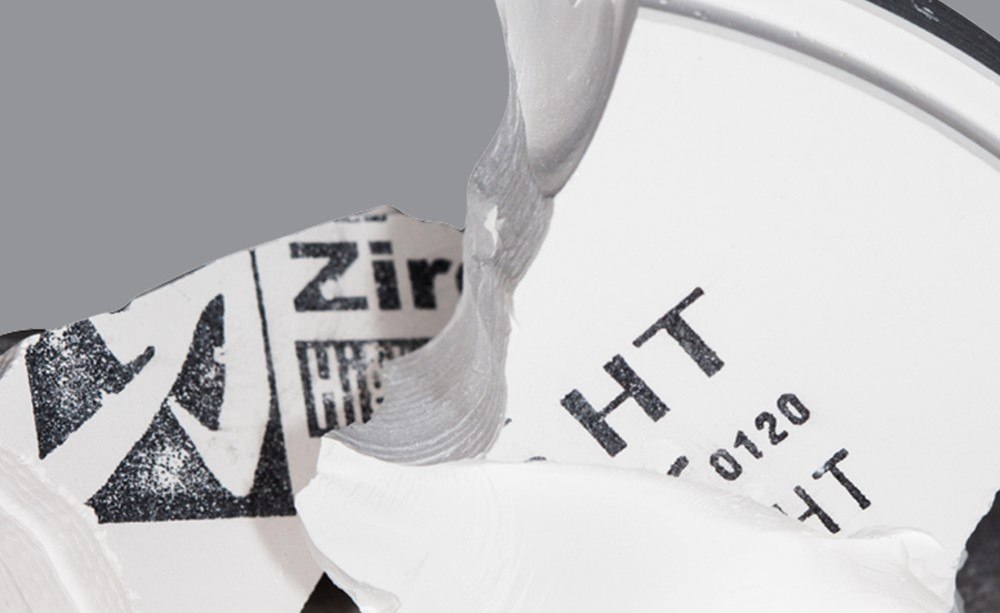
(Abb. 2) Reste eines weißen Zirkonoxid-Blanks nach dem Fräsen.
MoSi2 Heizelemente: Regeneration erforderlich
Erscheint eine Restauration grünlich oder gelblich, so liegt dies meist an alternden Heizelementen aus Molybdändisilizid (MoSi2) (Abb. 3). Diese benötigen entweder einen Regenerationsbrand oder sie sind auszutauschen. Das Innere der Heizelemente besteht aus Molybdän (Mo), das von einer Schutzschicht aus Siliziumoxid umgeben ist (Abb. 4). Die oxidische Schutzschicht baut sich normalerweise während des Sinterns bei Temperaturen zwischen 1.000 und 1.600 °C von alleine auf. Mit zunehmender Stärke der Schicht steigt deren Druckeigenspannung. Diese Spannung ist ebenso wie mögliche äußere Einflüsse –beispielsweise der Kontakt mit säurehaltigen Färbeflüssigkeiten – dafür verantwortlich, dass Risse entstehen und die Schutzschicht schließlich abplatzt. Durch diese Beschädigung wird das Molybdän im Inneren freigelegt. In einem als Pestoxidation bezeichneten Prozess reagiert das Molybdän im niedrigen Temperaturbereich von 400 bis 600 °C mit dem Sauerstoff in der Brennkammer. Dabei entsteht Molybdänoxid (MoO3), das gemeinsam mit Ionen und Metalloxiden aus Färbeflüssigkeiten die grün-gelblichen Verfärbungen auf der Restaurationsoberfläche verursacht.
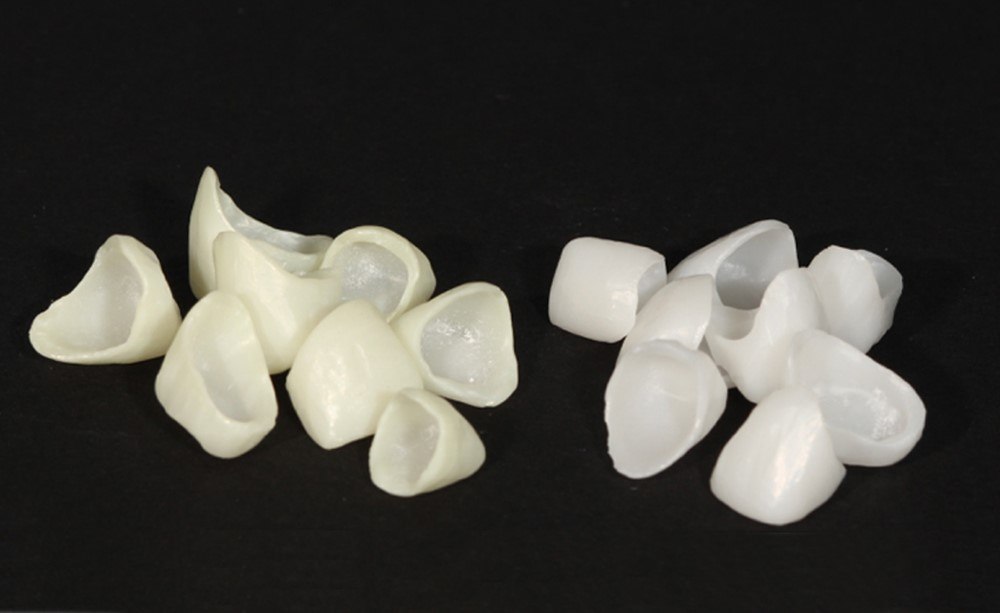
Abb. 3 Restaurationen mit grün-gelblichen Verfärbungen (links).
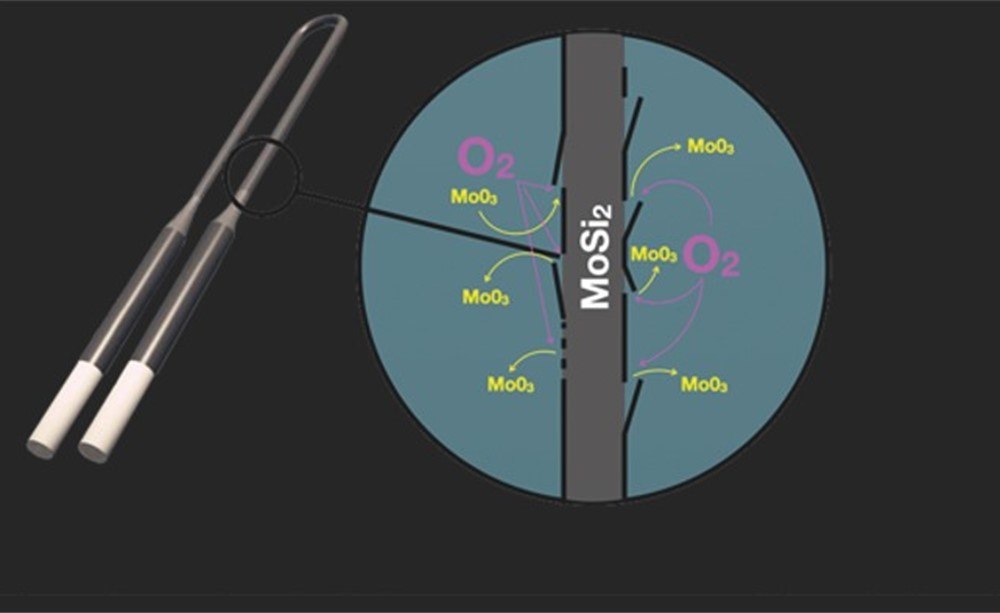
Abb. 4 Heizelement aus Molybdändisilizid mit abplatzender Schutzschicht aus Siliziumoxid. Diese verursacht die Pestoxidation sowie in der Folge eine Kontamination der Restaurationen im Sinterofen.
Eine Regeneration der Schutzschicht aus Siliziumoxid wird durch einen Regenerationsbrand mit schneller Aufheizrate und langer Haltedauer der finalen Brenntemperatur von rund 1.450 °C angestrebt. Diese Maßnahme funktioniert allerdings nur einige Male, da jede Pestoxidation und anschließende Regeneration die Heizelemente altern lässt. Am Ende bleibt der Austausch dieser die einzige Option. Das gesamte Problem der Pestoxidation kann durch den Einsatz von Öfen mit Heizelementen aus Siliciumcarbid (SiC) vermieden werden: Diese sind sehr alterungsbeständig und verursachen keine Verfärbung des Brennguts. Ein positiver Nebeneffekt: Diese Art Heizelemente liefern konstantere Brenntemperaturen.
Temperaturkontrolle
Veränderungen der Transluzenz oder der Farbsättigung und Pigmentierung der Restaurationsoberflächen sind häufig auf Abweichungen der tatsächlichen von den empfohlenen Sintertemperaturen zurückzuführen. Die einzige Möglichkeit, dieses Problem zu lösen, ist die Kalibrierung der Temperatur (Abb. 5). Diese Maßnahme ist nicht nur Voraussetzung für ästhetische Ergebnisse, sondern sie hat auch einen entscheidenden Einfluss auf die mechanischen Eigenschaften der Restaurationen: Ist die Endtemperatur zu hoch, führt dies beispielsweise meist zu einer Verringerung der Biegefestigkeit von Zirkonoxid1.
Die Überprüfung der Temperatur erfolgt üblicherweise mithilfe von TempTABs oder PTC-Ringen (PTC = process temperature control). Sie werden auf einer Sinterschale im Ofen platziert und durchlaufen einen vorgegebenen Kalibrierzyklus. Nach dem Sintern wird der Durchmesser des Tabs oder Rings bestimmt. Da sowohl TempTABs als auch PTC-Ringe kontrolliert schrumpfen, lässt sich die tatsächliche Sintertemperatur anhand des ermittelten Durchmessers errechnen (Abb. 6). Eine Umrechnungstabelle unterstützt Anwender dabei, die Abweichung zwischen der tatsächlichen und der am Ofen angegebenen Temperatur zu ermitteln. Falls notwendig, kann anschließend eine Anpassung der angegebenen Werte erfolgen.
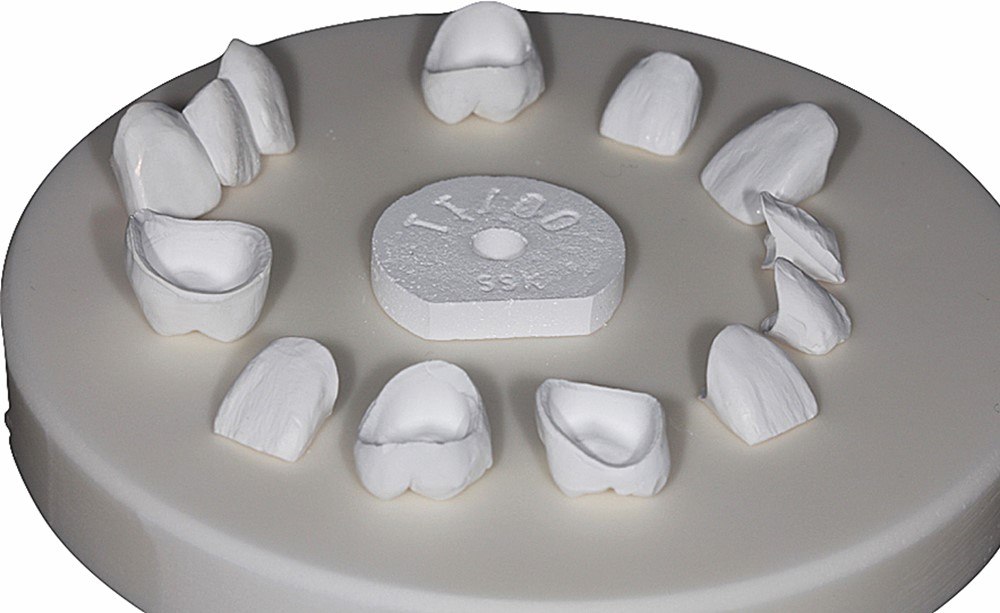
Abb. 6 TempTAB auf einer Sinterschale mit Restaurationen vor dem Sintern.
Generelle Empfehlungen
Um beste Voraussetzungen für eine brillante Ästhetik und optimale Eigenschaften von Restaurationen aus Zirkonoxid zu schaffen, sollten stets ideale Verarbeitungsbedingungen sichergestellt werden. Statt sich immer dann auf Fehlersuche zu begeben, wenn eine Restauration nach dem Sintern Verfärbungen aufweist, sollten Anwender die folgenden vorbeugenden Maßnahmen ergreifen:
- Reinigen des Wassertanks der Fräsmaschine vor jedem Fräsvorgang (nur bei Nassbearbeitung)
- Strikte Einhaltung der vom Materialhersteller empfohlenen Sinterprotokolle
- Entfernung von Staub in der Brennkammer und an den Heizelementen mit einer weichen Bürste vor jedem Einsatz
- Austausch von Sinterperlen aus Aluminiumoxid, sobald diese verfärbt sind (mindestens einmal monatlich)
- Verwenden von feinkörnigen Diamantinstrumenten für das Abtrennen der Anstiftelemente und die Oberflächenbearbeitung vor dem Sintern
- Falls möglich: Einsatz eines Sinterofens mit Heizelementen aus Siliciumcarbid
- Regelmäßige optische Kontrollen und Regenerationsbrände bei Öfen mit Heizelementen aus Molybdändisilizid
- Dekontaminationsbrands mit Resten weißen Zirkonoxids (y-TZP) oder speziellem Dekontaminationspulver (mindestens einmal monatlich)
- Überprüfung und Anpassung der Sintertemperatur (mindestens einmal monatlich)
Mit diesen einfachen Maßnahmen ist es möglich, das Potenzial von Multi-Layered-Zirkonoxiden voll auszuschöpfen.
KATANA Zirconia Multi-Layered
Einfach schön – die Geschichte von KATANA Zirconia (Kuraray Noritake) ist geprägt von der Begeisterung für Vollkeramik und der Leidenschaft für Ästhetik. Der Zustand der Rohstoffe, die Reinheit der Pulvermischung sowie die Homogenität und Dichte der Rohlinge – die Werkstoffeigenschaften sind gezielt aufeinander abgestimmt. Im Zusammenspiel mit einem sorgfältig aufgebauten Inhouse-Herstellungsprozess entsteht die hohe Materialqualität, für die KATANA Zirconia bekannt und beliebt ist. Das Zirkonoxid wird aus einer patentierten Rohstofftechnologie hergestellt, wobei selbst das Rohmaterial aus dem eigenen Hause kommt. Gegenüber den meisten anderen Zirkonoxidherstellern ist das ein klarer Vorteil, denn dies ermöglicht die minutiöse Abstimmung jedweder Parameter (Abb. 7). Bis ins kleinste Detail werden die Variablen für eine zuverlässige Anwendung optimiert. Die hohe Farbtreue macht KATANA Zirconia Multi-Layered so unverwechselbar, genau wie die Präzision und Perfektion, die das Material bietet. Zahntechnikerinnen und Zahntechniker profitieren durch hohe Wirtschaftlichkeit und Produktivität. Zudem sorgt die Zuverlässigkeit in Sachen Farbtreue und Präzision für ein entspanntes Arbeiten. In einer Scheibe steckt die volle meisterliche Kompetenz zahntechnischer Spezialisten!
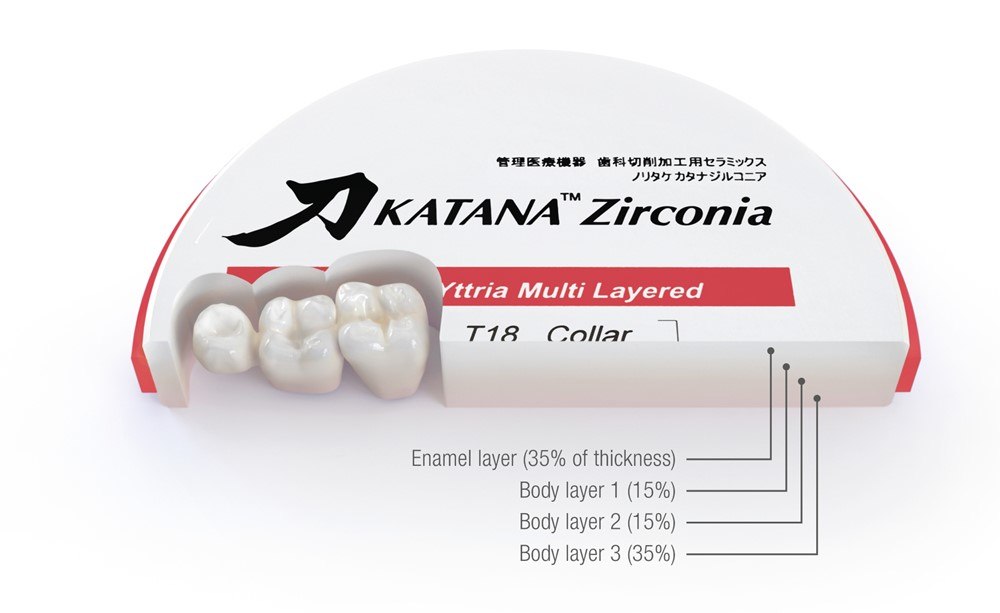
Abb. 7 Pionier der Multi-Layered-Zirkonoxide ist Kuraray Noritake. Das Unternehmen brachte im Jahr 2017 das erste mehrschichtige Zirkonoxid (KATANA Zirconia) auf den Markt. Heute besteht die KATANA Zirconia Multi-Layered aus verschiedenen Zirkonoxiden. Neueste Entwicklung ist das Multi-Generationen-Material KATANA Zirconia YML.
Literatur
1 Stawarczyk, B., Özcan, M., Hallmann, L. et al. The effect of zirconia sintering temperature on flexural strength, grain size, and contrast ratio. Clin Oral Invest 17, 269–274 (2013).
Titelfoto: adobe.stock.com/Antonio