Der Auftrag an unser Labor lautete: Anfertigung einer Großserie von insgesamt 800 Konstruktionen für den Oberkiefer, und zwar zu gleichen Teilen aufgeteilt auf
- Einzelzahn für die Front
- Frontzahnbrücken vom 1er bis zum 3er und
- Frontzahnbrücken vom 3er bis 3er mit Cutback
Masse mit Klasse
Zu jeder Konstruktion sollte ein gedrucktes Modell inklusive gedrucktem Logo gehören. Die dazugehörende Materiallieferung umfasste 47 Zirkonblanks in verschiedenen Farben: 28x 14 mm, 7x 22 mm, 12x 18 mm). Für die Umsetzung kamen in unserem Labor folgende Materialien und Maschinen zum Einsatz:
- Next Dent Model 2.0 Peach
- Next Dent 5100 von Amann Girrbach
- Sheraprint-gingiva mask
- Ethanol
- Shera Print-wash
- Amann Girrbach Ceramill Matik
- Amann Girrbach Therm3
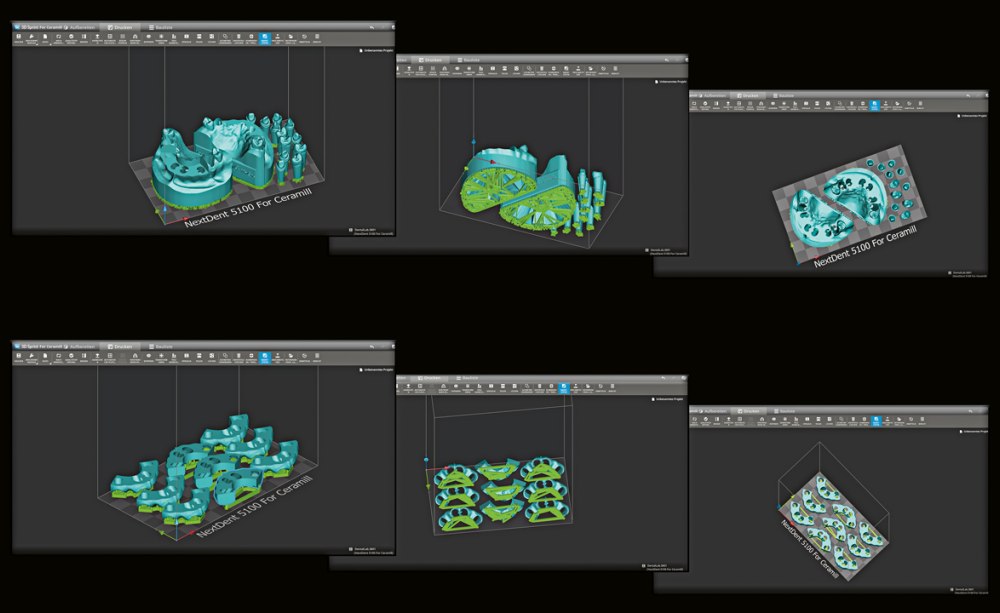
Angesichts der großen Zahl zu druckender Elemente spielte effizientes Nesting eine entscheidende Rolle.
Zu Beginn unserer Planung stellten sich zahlreiche Fragen: Wie viele Konstruktionen sind mit den gelieferten Blanks überhaupt möglich? Wie gestaltet man die Aufteilung der Konstruktionen hinsichtlich der unterschiedlichen Höhen? Wie müssen die Modelle aussehen? Welche Geräte benötigen wir für den Auftrag? Welche zusätzlich erforderlichen Materialien müssen in welchen Mengen bestellt werden?
Modelldruck und Konstruktion
Unser Ziel war es, möglichst ein Modell zu haben, das als Standard für alle gewünschten Konstruktionen verwendet werden kann. Also haben wir in unserem „Patienten-Archiv“ gesucht und wurden dort auch fündig. Zunächst wurde ein erstes Testmodell für die 1er-Krone bearbeitet und digital hergestellt. Nach Absprache im Team wurde uns allerdings klar, dass das Ergebnis unbefriedigend war – wir wollten mehr Ästhetik und schärfere Kanten. Einzige Lösung: Die eigene Herstellung perfekter Grundmodelle aus Gips. Wir begaben uns also erneut auf die Suche nach einem vollbezahnten Modell, welches wir nach unseren Ansprüchen umgestalten konnten. Das vorhandene Modell wurde in ausreichender Zahl doubliert, um für jede Konstruktion ein eigenes Modell zur Bearbeitung zu haben. Da sich die gefrästen Teile auf die Frontzähne beschränkten, verkleinerten wir das Modell von 15 nach 25. Die gewünschten Zähne wurden radiert, die Stümpfe präpariert und das Modell nach unseren Wünschen und Vorstellungen bearbeitet – keine leichte Aufgabe, aber wir meisterten sie in Teamarbeit.
Der digitale Prozessschritt
Als nächstes ging es an den digitalen Prozessschritt, und dort ergab sich erneut eine Vielzahl an Fragen: Ist es möglich, auf Stumpfmodellen eine abnehmbare Gingiva herzustellen? Ursprünglich sieht die Software derartige Konstruktionen nur bei Implantat-Modellen vor. Können wir ein Logo auf das Modell bringen? Woher bekommen wir dieses und welches Dateiformat muss es haben? Es folgte die Kontaktaufnahme zu Noritake. Wir berichteten von unserem Plan, und kurze Zeit später war die entsprechende Datei im Postfach unseres E-Mail-Accounts: das Kuraray-Noritake-Logo im STL-Format.
Nach einer weiteren Recherche im Internet, einem Ceramill-Update von Amann Girrbach und einigen Konstruktionsversuchen fanden wir schließlich einen Weg, eine Gingiva auch ohne Implantate zu konstruieren. Nachdem diese Hürde überwunden war, stellten wir fest, dass es Unterschiede bei den Stumpfpins gibt, je nachdem, ob die Krone vor dem Modell designt wird oder danach. Es stellten sich also zwei Vorgehensweisen heraus:
- Gipsmodell einscannen, in der Ceramill Mind von Amann Girrbach eine Präpgrenze festlegen, Krone designen und danach ein digitales Modell kreieren – der Stumpfpin weist eine Hohlkehle unterhalb der Präparationsgrenze auf.
- Gipsmodell einscannen, digitales Modell kreieren, danach auf diesem Modell eine Krone konstruieren – der Stumpfpin verläuft senkrecht ab der Präparationsgrenze und der Spalt zwischen Gingiva und Präparationsgrenze wird nicht übernommen.
Wir entschieden uns für die erste Alternative, da uns der Pin eindeutig besser gefiel. Danach stand dem Start für Probedrucke für das 1er- und 3er-Brücken-Modell nichts mehr im Wege. Konstruiert wurde in der Amann-Girrbach-Software Model Creator. Da es dort leider nicht möglich ist, für jeden einzelnen Stumpf des Modells eigene Passungsparameter einzustellen, mussten wir zunächst testen, auf welchen Wert wir uns zu beschränken hatten, um möglichst wenig Nacharbeit am Modell vornehmen zu müssen, um die Stümpfe aufzupassen. Damit eine perfekte Passung der Kronen auf dem Modell sichergestellt ist, ist es wichtig, einen Spalt zwischen dem Modell und der Präparationsgrenze einzustellen. Dieser Spalt schafft Platz für die Materialstärke der Zirkonkrone.
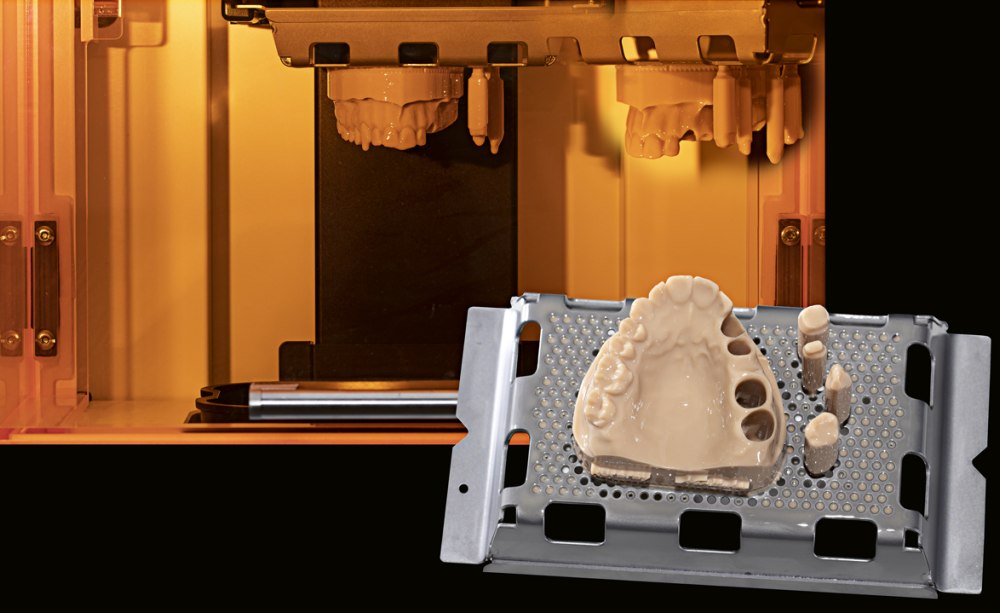
Der 3-D-Drucker Next Dent 5100 von Amann Girrbach lief bei der Neodent Zahntechnik im Dauereinsatz.
Nachdem wir die 1er- und 3er-Brücken-Modelle perfektioniert hatten, wurden diese mit dem Map600 von Amann Girrbach eingescannt und in der Ceramill Mind von Amann Girrbach konstruiert. Auch hier galt es, Testfräsungen durchzuführen. Ziel war es, ein gleichbleibendes Ergebnis aller Kronen und Brücken für ein möglichst geringes Maß an Nacharbeit zu erreichen. Für die Konstruktion diente die Spieglung des anderen Quadranten, um ein Maß für Form und Größe zu erhalten. Die Testfräsungen dienten der Kontrolle der Approximalkontakte und des Kronensitzes sowie – mit Blick auf die Serienproduktion – dem Verschleiß der Fräser und eventuellen Veränderungen beim Druckergebnis durch Reinigung der Stümpfe und des Modells.
Neben den Testläufen lief gleichzeitig die Projekt- und Zeitplanung für den Auftrag:
- ungefähre Abschätzung, wie viel Druckmaterial benötigt wird
- Berechnung, wie viele Konstruktionen wir aus den Blanks fertigen können und somit auch die Anzahl der nötigen Modelle.
- Ermittlung der maximalen Zahl der Modelle, die auf die Druckplattform des Nextdent 5100 passen
- Ermittlung der erforderlichen Druckzeiten
- Abschätzung, wie viele Modelle an einem Tag produziert werden können
- Abschätzen des Zeitbedarfs für die Nacharbeit und Reinigung
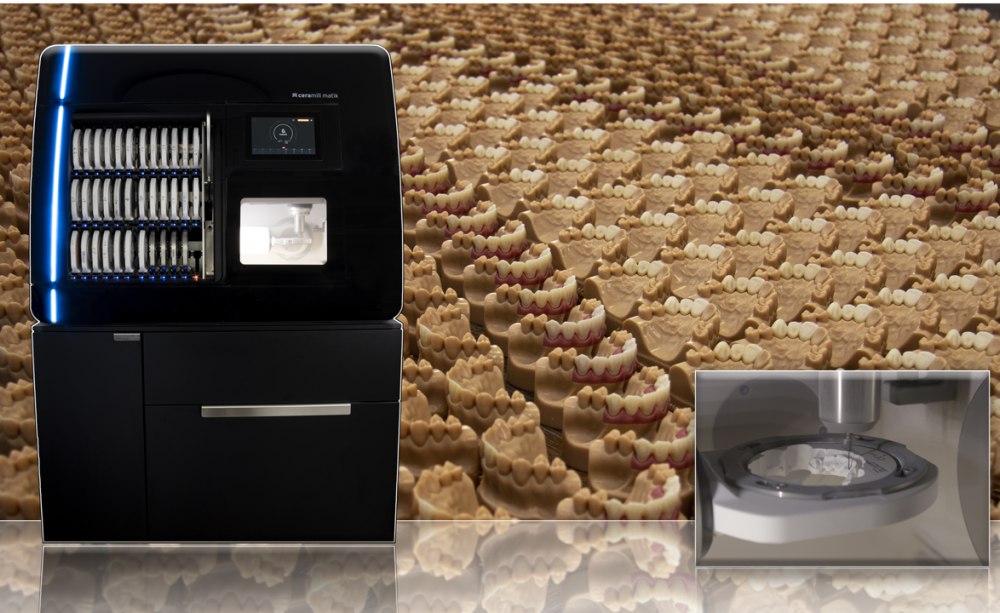
Die Ceramill Matik von Amann Girrbach lief nachts und an den Wochenenden unter Volllast.
Nacharbeit und Aufwand reduzieren, aber wie?
Relativ schnell stellte sich heraus, dass uns die generelle Nacharbeit der Modelle, vor allem ihre Reinigung, sehr viel Zeit rauben würde. Wir erkundigten uns nach einer Alternative zum händischen Säubern. In diesem Zusammenhang stießen wir auf die Print-Wash von Shera. Dieses automatische System sollte uns die Reinigung der gedruckten Modelle abnehmen und eine gleichbleibende Qualität mit annähernd perfektem Ergebnis sichern. Nach kurzer Recherche und Beratung durch Shera-Mitarbeiter entschieden wir uns dafür, diese Reinigungseinheit in unseren Laborbestand aufzunehmen. Eine riesengroße Hilfe, denn nach dem Druckvorgang und Entfernen der Stützstrukturen kann das gedruckte Objekt direkt in die Print-Wash gegeben werden und wird darin mit zwei Reinigungsdurchläufen vom restlichen Druckmaterial befreit. Das Modell 2.0 muss laut Hersteller mit mehr als 90-prozentigem Ethanol gereinigt werden, welches nach zwölf Waschgängen gewechselt werden muss, um unseren Leistungsansprüchen gerecht zu werden.
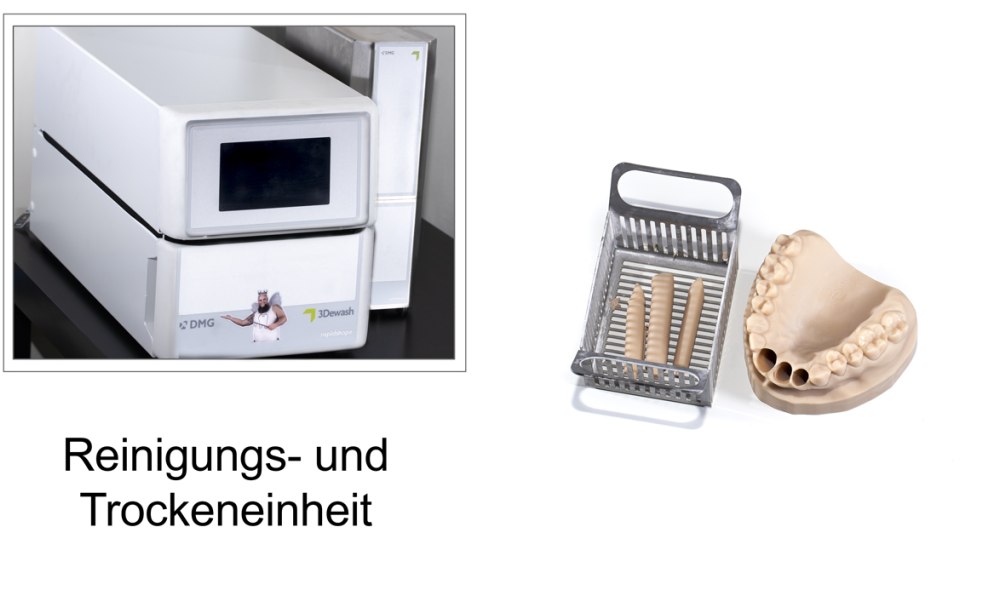
Ohne die Reinigungs- und Trockeneinheit Shera Print-wash wäre die Zahl von 800 Modellen nicht realisierbar gewesen.
Konstruktion der ersten 1er- und 3er-Brücken
Für die 1er- und 3er-Brückenkonstruktionen verwendeten wir die Blanks in 14er Höhe, um diesen möglichst in der Höhe auszufüllen und der sechsgliedrigen Brücke genug Platz für die Neigung in den 18er und 22er Höhen zu lassen. Nach Berechnung der Konstruktionen und Modelle konnte die Produktion starten. Der Drucker lief pausenlos, im normalen Arbeitsalltag mit Unterstützung eines Weckers, der uns im immer gleichen Zeitabstand daran erinnerte, den nächsten Druckauftrag zu starten.
Die Ceramill Matik von Amann Girrbach lief nachts und an den Wochenenden regelrecht heiß. Der Sinterofen war in der Woche tagsüber mit den Noritake-Kronen beschäftigt und nachts mit unseren Kundenarbeiten. Das Wichtigste war, eine immer gleichbleibende Qualität der Fräs- und Druckergebnisse zu sichern. Deshalb perfektionierten wir jeden Arbeitsschritt und wichen nie von der etablierten Arbeitsabfolge ab.
Auf zum sechsgliedrigen Brückenmodell
Bei diesem Modell wollten wir gerne eine abnehmbare Gingiva hinzufügen, um dem Modell einen weiteren Zugewinn an Ästhetik geben zu können. Gesagt, getan, getestet – und die erste Herausforderung war schon da: Der gewünschte Abstand zwischen Modell und Stumpf ließ sich im Modell Creator von Amann Girrbach leider nur ohne Gingiva einstellen. Sobald die Software eine Gingiva berechnete, wurde die Einstellung des Abstands nicht übernommen. Also Krisensitzung … Wir wollten unbedingt die Gingiva dazu drucken, aber bei hunderten von Modellen alle händisch schleifen? Auf keinen Fall! Also musste eine andere Software her … und zwar schnell, denn die Zeit lief uns davon.
Nach vielen verschiedenen Tests mit möglichen Modellsoftware-Lösungen und zahlreichen Gesprächen mit Kollegen aus anderen Laboren wurden wir schließlich fündig. Man stellte uns den Modelbuilder von Shera mit einer 30-tägigen Testlizenz zur Verfügung. Mit der Software waren wir bereits nach wenigen Versuchen vertraut. Jeder Stumpf ist individuell einstellbar, eine abnehmbare Gingiva konstruierbar und der für uns so wichtige Abstand zwischen Gingiva und Stumpf ist verstellbar! Auf den ersten Blick gab es zwar leider keine Möglichkeit, ein Logo anzubringen, aber auch für dieses Problem fanden wir nach ein paar Versuchen eine Lösung.

Das Ergebnis: Einzelzahn für die Front, Frontzahnbrücke vom 1er bis zum 3er und Frontzahnbrücke vom 3er bis 3er mit Cutback auf 3-D-gedruckten und polierten Modellen mit abnehmbarer Gingiva und eingedrucktem Logo.
30 Tage brauchten wir für ein perfektes Modell mit entsprechender Konstruktion der sechsgliedrigen Brücke. Für die Gingiva testeten wir verschiedenste Materialien. Nach kurzer Beurteilung durch unser Team fiel die Entscheidung für das Material SheraPrint-gingiva, da der Farbton deutlich ästhetischer und das Material flexibler ist. Nebenbei bemerkt lässt es sich auch wunderbar beschleifen.
Nach vielen Testdurchläufen und entsprechenden Änderungen an Modell und Gingiva fehlte uns schließlich immer noch der „Wow“-Effekt, und so probierten wir, die Modelle und Gingiva auf Hochglanz zu polieren. Und siehe da, das Ergebnis stellte uns mehr als zufrieden. Also polierten wir alle 800 Modelle und die dazugehörigen Gingivamasken per Hand am Poliermotor!
Für die sechsgliedrige Konstruktion wurden ebenfalls Testfräsungen durchgeführt, um ein bestmögliches und gleichmäßiges Ergebnis bei gleichzeitig geringstem Aufwand zu bekommen. Bei dieser Konstruktion war deutlich zu spüren, dass nicht jedes gedruckte Modell gleich ist. Was bei kleineren Konstruktionen nicht so sehr ins Gewicht fällt, wurde uns hier aufgrund der hohen Stückzahlen umso deutlicher gezeigt. Allein der Druck, die Säuberung der Modelle oder auch die Qualität der herausnehmbaren Stümpfe haben Einfluss auf die Passung der Konstruktion. Hinzu kam die abnehmbare Gingiva …
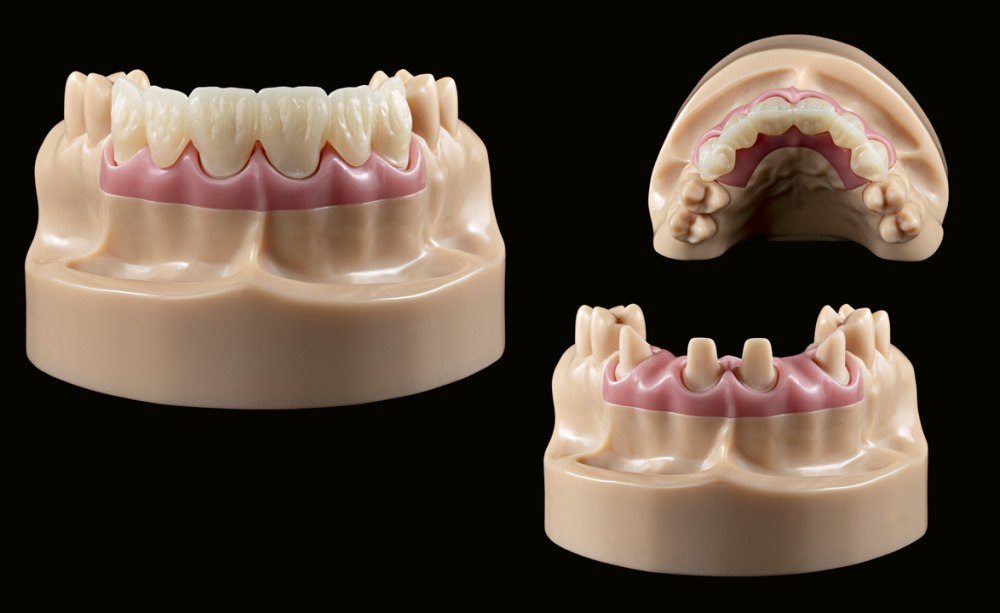
Frontzahnbrücke vom 3er bis 3er auf poliertem Modell
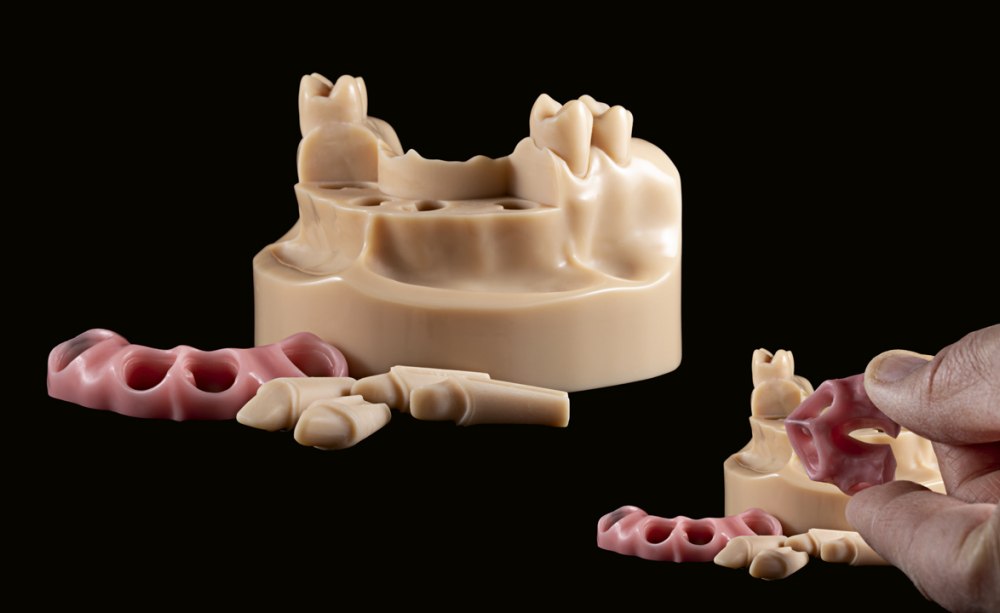
Alle Optionen wie abnehmbare Gingiva und herausnehmbare Stümpfe konnten in einem Modell realisiert werden.
Somit war die sechsgliedrige Brücke in Bezug auf gleichbleibende Passung noch einmal eine große Herausforderung. Wir begannen die Testfräsungen nach einem Wert für Approximalkontakte und Kontakt zur Gingiva. An der Passung der Stümpfe in Bezug auf eventuellen Verzug aufgrund der Größe und des Frontzahnbogens innerhalb des Sinterprozesses gab es nichts auszusetzen, jedoch merkten wir schnell, welches Modell perfekt gedruckt war und welches nicht.
So schön die Ergebnisse auch waren, der Abgabetermin rückte immer näher. Neben dem Tagesgeschäft war dieser ungewöhnliche Auftrag eine logistische Herausforderung für uns. Das gesamte Projekt forderte uns einerseits unerwartet viel Kraft, dafür war andererseits der Lerneffekt enorm. Für die Zukunft wissen wir nun, dass eine ordentliche Projektplanung, eine saubere Kostenkalkulation und engmaschige Absprachen im Team unabdingbar sind.
800 Konstruktionen und Modelle – in sechs Wochen
Im Ergebnis standen wir vor 800 eigenhändig erstellten Modellen, alle per Hand bearbeitet und poliert, sowie vor 800 dazugehörigen Konstruktionen, die aus 47 Blanks herausgetrennt und bearbeitet wurden. Das alles bewältigten wir innerhalb von sechs Wochen neben unserer alltäglichen Arbeit. Man könnte sagen, wir seien verrückt, aber am Ende waren wir nur unfassbar stolz auf uns. Dank dieses Großauftrags war es uns möglich, viele Schwierigkeiten zu erkennen, auf die wir im normalen Laboralltag wahrscheinlich nicht gestoßen wären. Wir haben neue Software und Geräte kennengelernt, die uns auch den heutigen Arbeitsablauf erleichtern, und Probleme erkannt, die selbst die Hersteller nicht im Blick hatten. Am meisten haben wir uns im Bereich 3-D-Druck weiterentwickelt und an Know-how gewonnen. Wir haben die Herausforderung gemeistert, bei 800 Modellen und dazugehörigen Konstruktionen ein perfektes Ergebnis zu erzielen, und haben erfahren, wie viele unterschiedliche Einflüsse dort hineinspielen. Wir sind sehr froh darüber, dass wir einen so großen Auftrag bekommen haben und so viel daraus lernen durften.
Kontakt:
Neodent Zahntechnik GmbH
Kaiser-Friedrich-Straße 90
10585 Berlin
Telefon: (030) 28 88 81 88
E-Mail: info@neodent-zahntechnik.de
Web (demnächst): neodent-zahntechnik.de